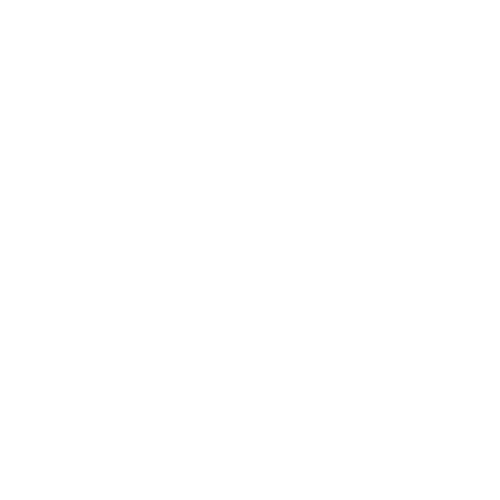
The global demand for dried cassava chips has surged in recent years, driven by China’s growing need for bio-ethanol production, food products, and animal feed. This presents a golden opportunity for African cassava producers to expand their market reach and boost economic growth. Chinese manufacturers are willing to order between 50,000 to 100,000 metric tons (MT) of dried cassava chips per month, with contracts spanning 3 to 5 years. However, despite this immense potential, African exporters face significant challenges that hinder their ability to fully capitalize on this opportunity.
This article explores the key challenges African cassava producers face in exporting to China and provides actionable strategies to overcome them. By addressing these obstacles, Africa can position itself as a competitive player in the global Cassava market and unlock its vast agricultural potential.
1. Enhancing Price Competitiveness of African Dried Cassava Chips
One of the most pressing challenges for African cassava exporters is the higher cost of their product compared to competitors from Southeast Asia. The average CIF (Cost, Insurance, and Freight) price of African dried cassava chips is around $400 per MT, while Southeast Asian suppliers offer prices as low as $320 per MT. To bridge this gap, African producers must adopt cost-reduction strategies that enhance their competitiveness.
Successful Strategies and Lessons Learned:
- Scaling Up Production: Small-scale operations are a major contributor to high production costs. By investing in large-scale production facilities or forming cassava processing cooperatives, African producers can achieve economies of scale. For example, Nigeria’s cassava value chain transformation program has demonstrated that scaling up production can reduce costs by up to 20%.
- Adopting Modern Processing Technologies: Modern machinery, such as energy-efficient dryers, can significantly lower production costs. In Ghana, the introduction of solar-powered drying technologies reduced energy costs by 30%, making their cassava chips more competitive in international markets.
- Investing in Renewable Energy: Incorporating renewable energy solutions, such as solar or biomass, for processing facilities can provide long-term cost savings. A successful case in Tanzania saw cassava processors reduce energy costs by 40% after switching to solar-powered drying systems.
2. Navigating the GACC Certification Process
Exporting agricultural products to China requires certification from the General Administration of Customs China (GACC). The complexity and slow processing time of this certification process are significant barriers for African exporters.
Successful Strategies and Lessons Learned:
- Government-to-Government Cooperation: African governments can engage in bilateral negotiations with Chinese authorities to simplify and fast-track the certification process. For instance, Togo’s Ministry of Agriculture collaborated with the Chinese Embassy to expedite GACC approvals for Togolese exporters, reducing processing times by 50%.
- Capacity Building and Training: Exporters often struggle to meet Chinese regulatory standards. Industry associations and government bodies can provide targeted training programs. In Uganda, a government-led initiative trained over 500 cassava producers on GACC requirements, resulting in a 60% increase in successful certifications.
- Certification Support Services: Establishing local certification centers or partnering with GACC-accredited agencies can streamline the process. Kenya’s collaboration with a Chinese certification agency reduced documentation errors by 80%, accelerating the approval process.
3. Reducing High Transport Costs from Africa to China
Transport costs remain a significant challenge for African exporters, despite preferential shipping rates offered by COSCO. The lengthy sea routes and limited container availability further exacerbate the problem.
Successful Strategies and Lessons Learned:
- Consolidated Shipping: Exporters can collaborate to create shared shipping containers, reducing individual costs. In West Africa, a regional exporters’ association successfully implemented a consolidated shipping model, lowering transport costs by 25%.
- Strategic Use of Transshipment Routes: Shipping via hubs like Singapore or Dubai can reduce costs by leveraging economies of scale. A Nigerian exporter reduced shipping costs by 15% by using Dubai as a transshipment hub.
- Investing in Inland Logistics: Improving rural infrastructure and using low-cost transportation alternatives, such as rail or river transport, can lower logistics costs. Ethiopia’s investment in rural road networks reduced farm-to-processing site transport costs by 30%.
4. Reducing Production Costs for Fresh Cassava Roots
The cost of producing fresh cassava roots significantly impacts the overall pricing of dried cassava chips. High labor costs, low farm productivity, and inefficient transportation systems contribute to these challenges.
Successful Strategies and Lessons Learned:
- Adopting High-Yield Cassava Varieties: Investing in agricultural research and providing farmers with access to high-yield, drought-resistant cassava varieties can increase productivity. In Malawi, the introduction of high-yield varieties increased cassava production by 40%, reducing per-unit costs.
- Improving Farm-to-Market Infrastructure: Public investment in rural road networks can drastically reduce transportation costs. Rwanda’s investment in feeder roads reduced farm-to-market transport costs by 35%.
- Strengthening Cooperative Farming Models: Cooperative farming models enable smallholder farmers to pool resources, reducing production costs. In Cameroon, cassava cooperatives reduced input costs by 20% through bulk purchasing and shared equipment.
5. Addressing Post-Harvest Losses Through Better Storage Infrastructure
Fresh cassava roots are highly perishable, and the lack of storage infrastructure results in significant post-harvest losses. Addressing this issue is critical for improving the profitability of cassava production.
Successful Strategies and Lessons Learned:
- Investing in Cassava Storage Solutions: Solar-powered cold storage and low-cost silos can extend the shelf life of cassava roots. In Mozambique, the introduction of solar-powered storage reduced post-harvest losses by 50%.
- Supporting Post-Harvest Technology Development: Collaboration with agricultural universities and research centers can lead to innovative storage solutions. In Nigeria, the adoption of fermentation techniques reduced spoilage rates by 60%.
Conclusion
The challenges of exporting African dried cassava chips to China are significant but not insurmountable. By adopting cost-reduction strategies, navigating the GACC certification process, and investing in modern storage and processing technologies, African cassava producers can enhance their competitiveness in the global market. Collaborative efforts between governments, industry stakeholders, and the private sector are essential to overcoming these challenges and tapping into the enormous demand for cassava in China.
Africa’s cassava industry has the potential to become a major player in the global market, driving economic growth and creating jobs across the continent. With the right strategies and investments, African exporters can transform challenges into opportunities and secure a prosperous future for the cassava value chain.
I hope you enjoyed reading this post and learned something new and useful from it. If you did, please share it with your friends and colleagues who might be interested in Agriculture and Agribusiness.
Mr. Kosona Chriv
Founder of LinkedIn Group « Agriculture, Livestock, Aquaculture, Agrifood, AgriTech and FoodTech » https://www.linkedin.com/groups/6789045/
WhatsApp: +234 904 084 8867
LinkedIn: linkedin.com/in/kosona
Co-Founder, Chief Operating Officer and Chief Sales and Marketing Officer
Deko Integrated & Agro Processing Ltd
IDUBOR HOUSE, No. 52 Mission Road (by Navis St.)
Benin City, Edo State, Nigeria | RC 1360057
Group Chief Sales and Marketing Officer
SOLINA GROUPE CÔTE D’IVOIRE
Cocody, Riviera Bonoumin
Lot 738 Ilot 56 Section ZT parcelle 67
11 BP 1085 Abidjan 11
Ivory Coast


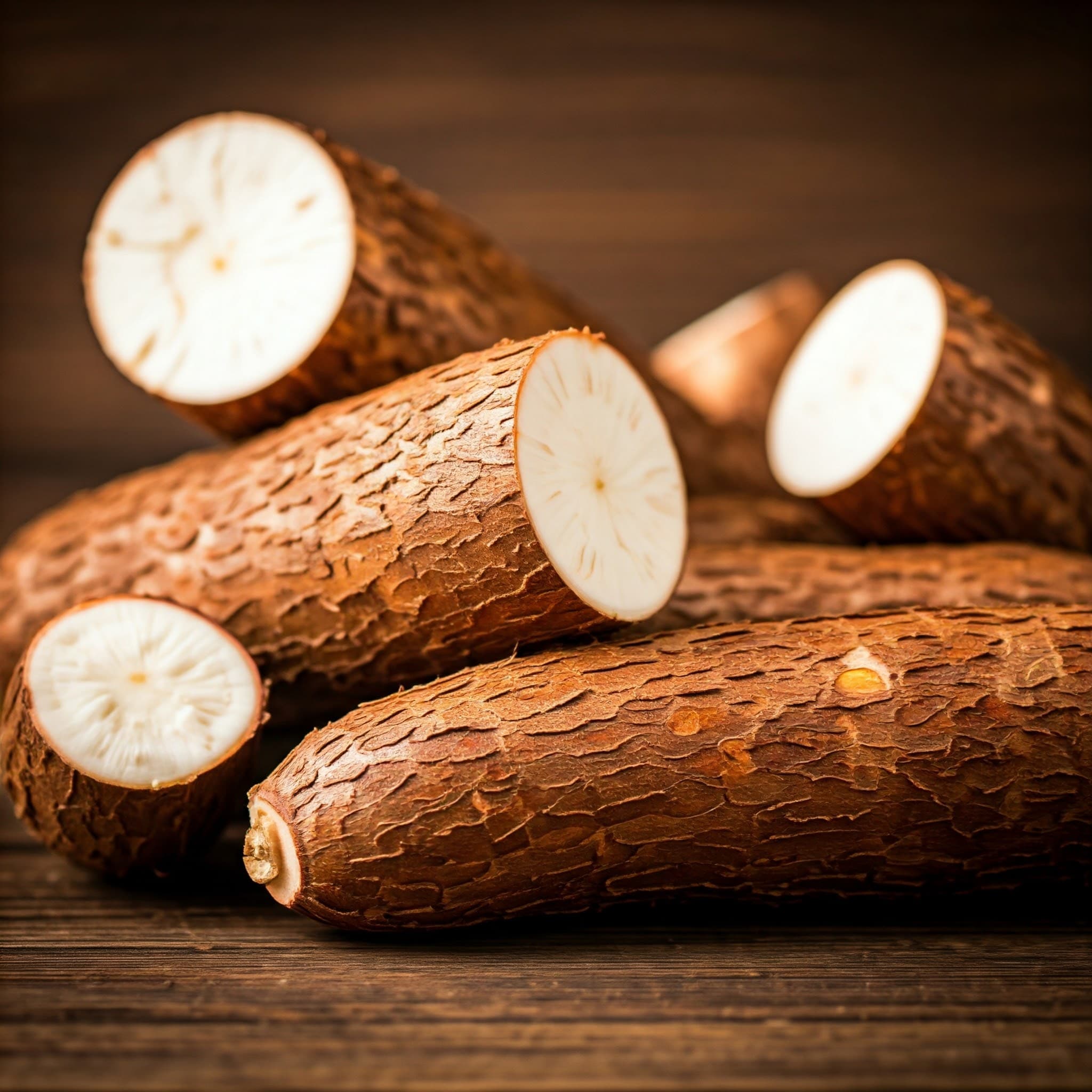
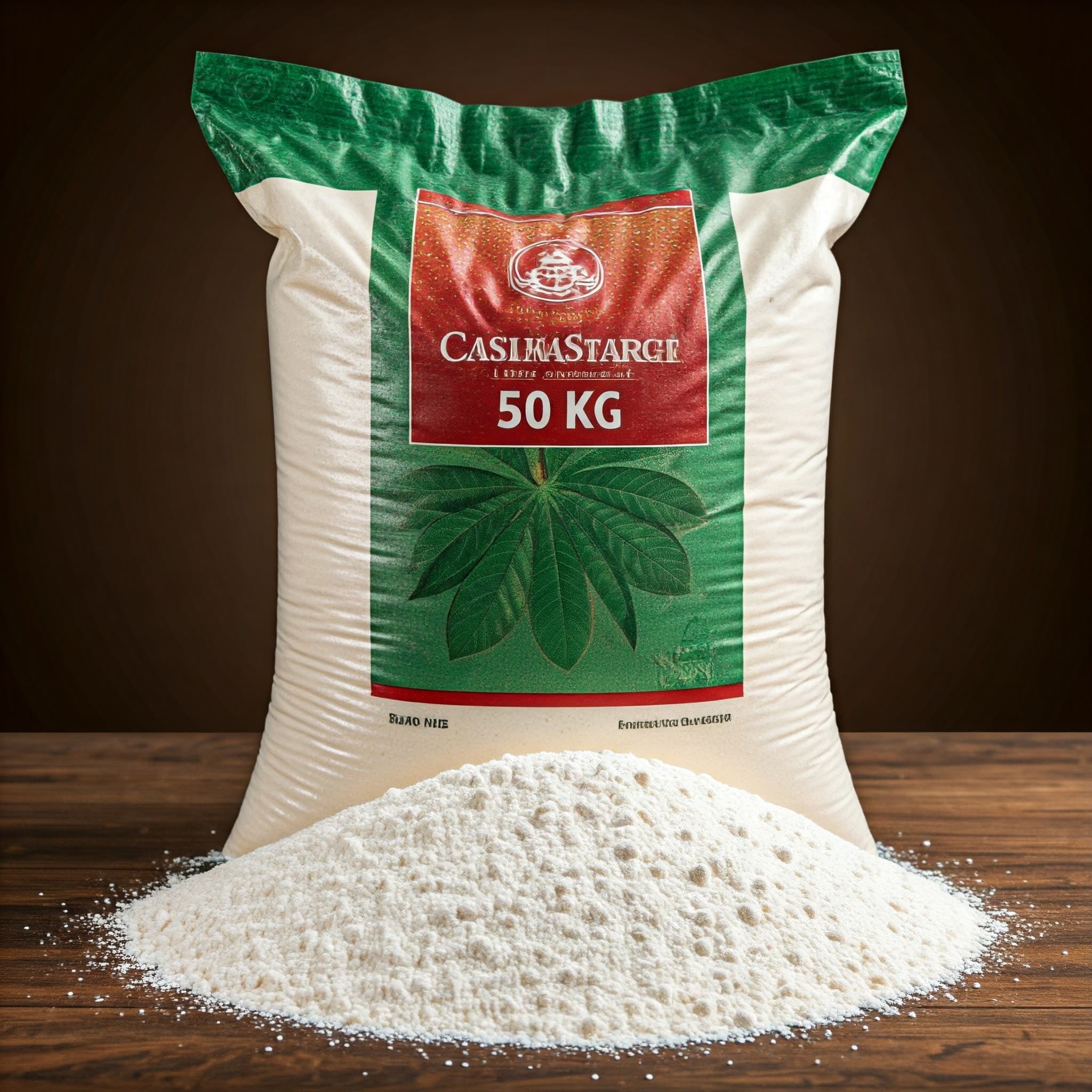
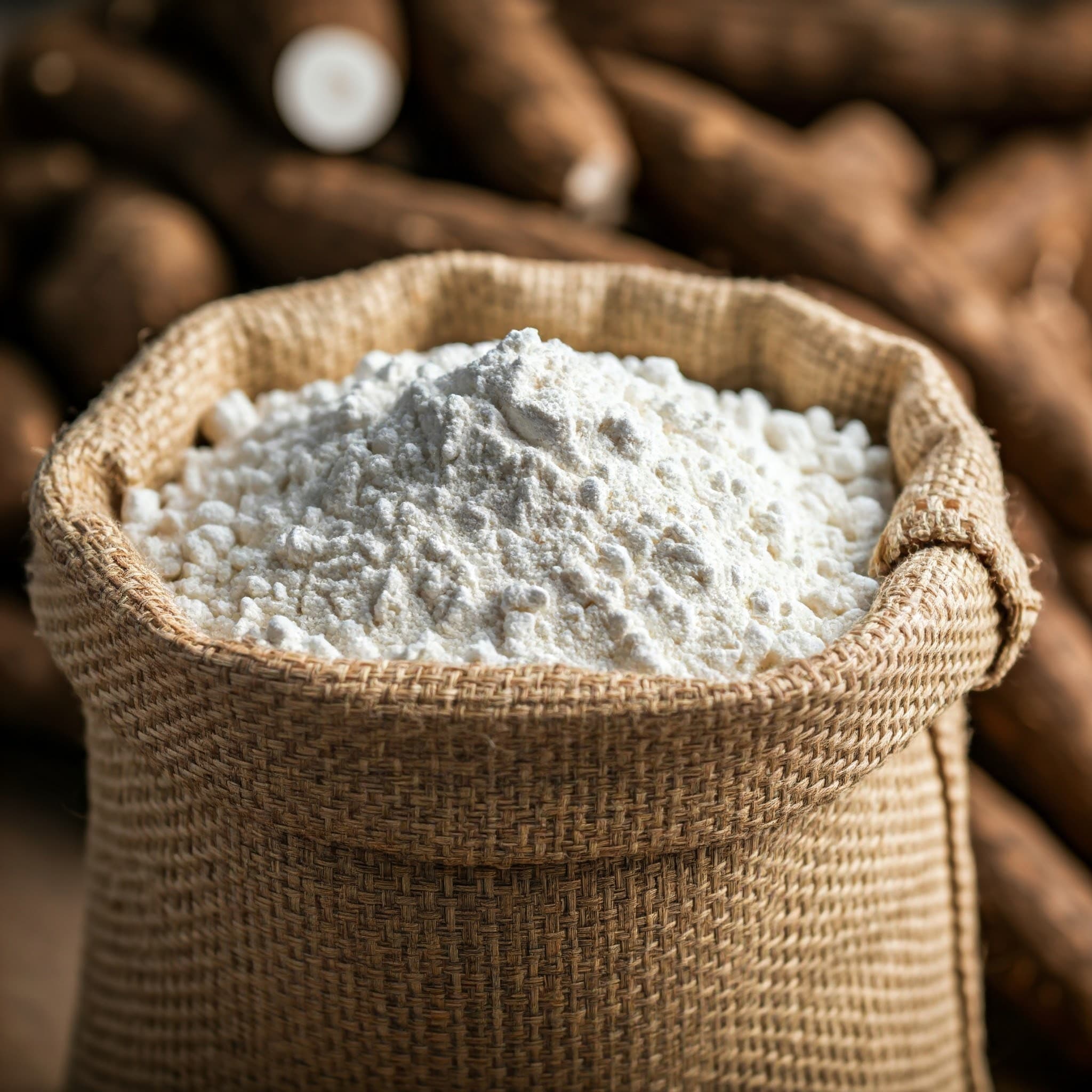
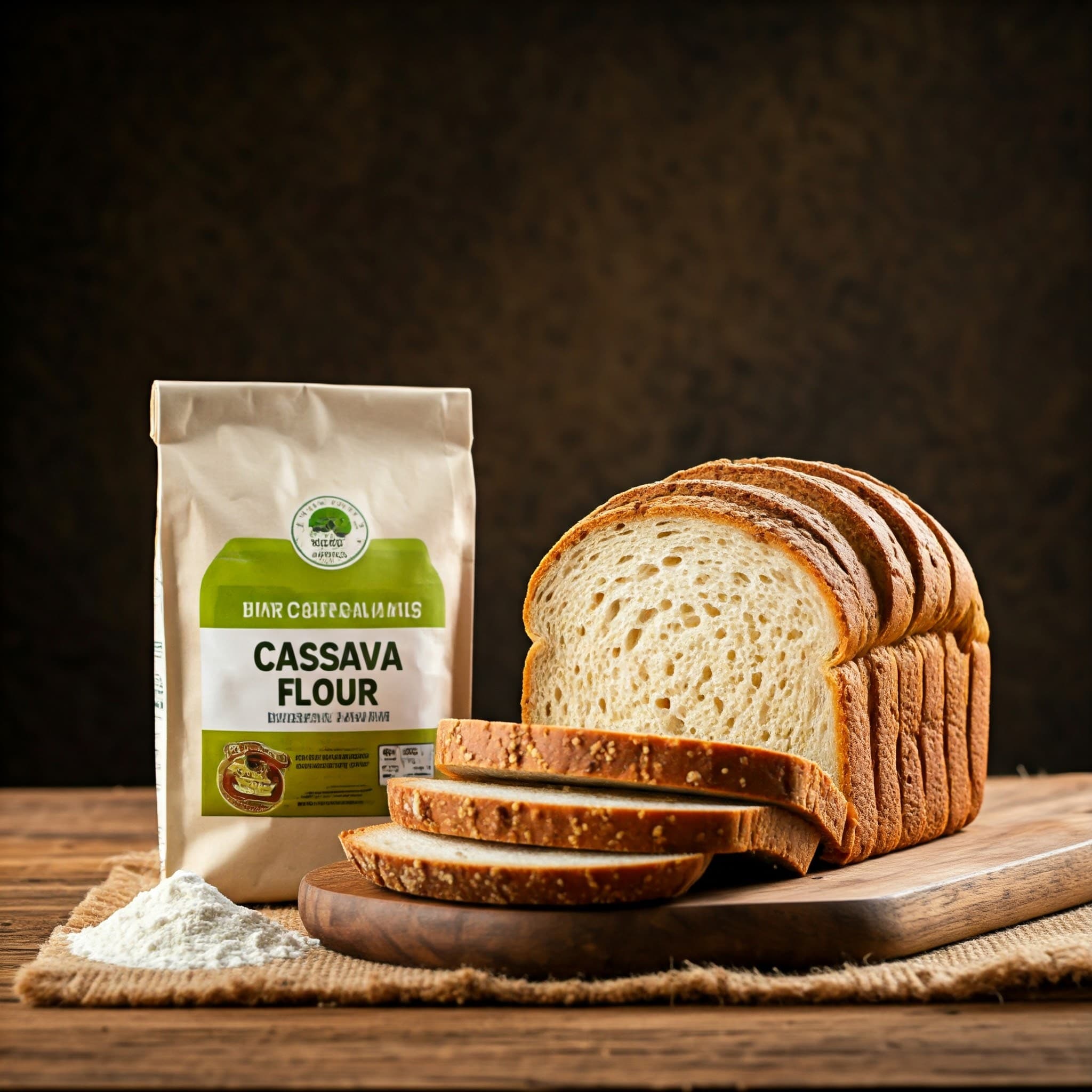
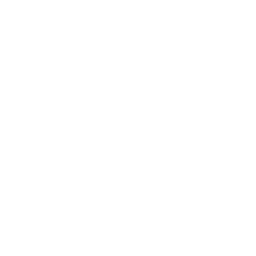
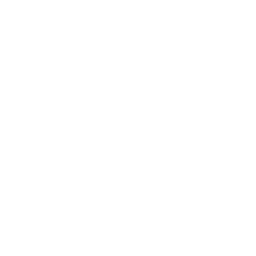
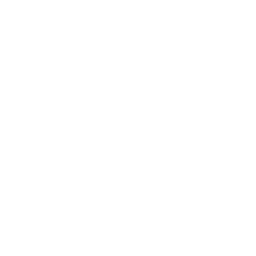
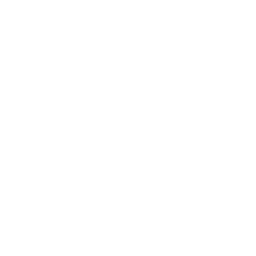
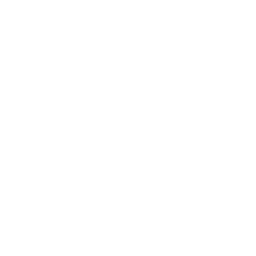
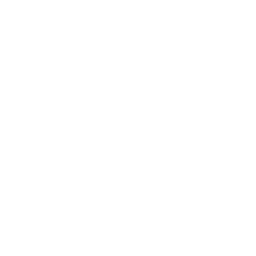
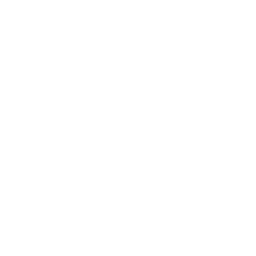
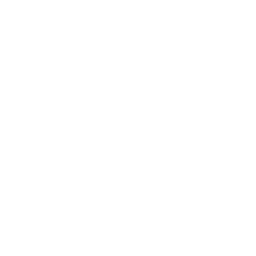
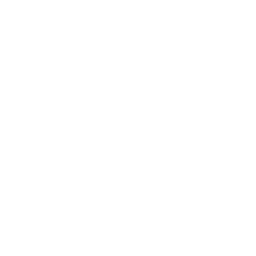
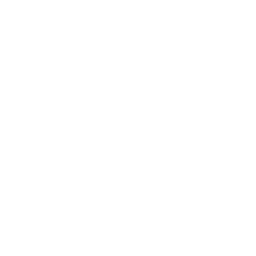
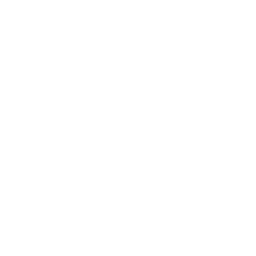
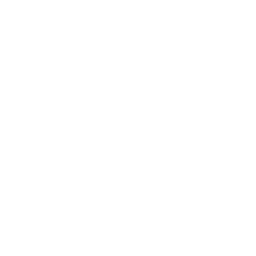